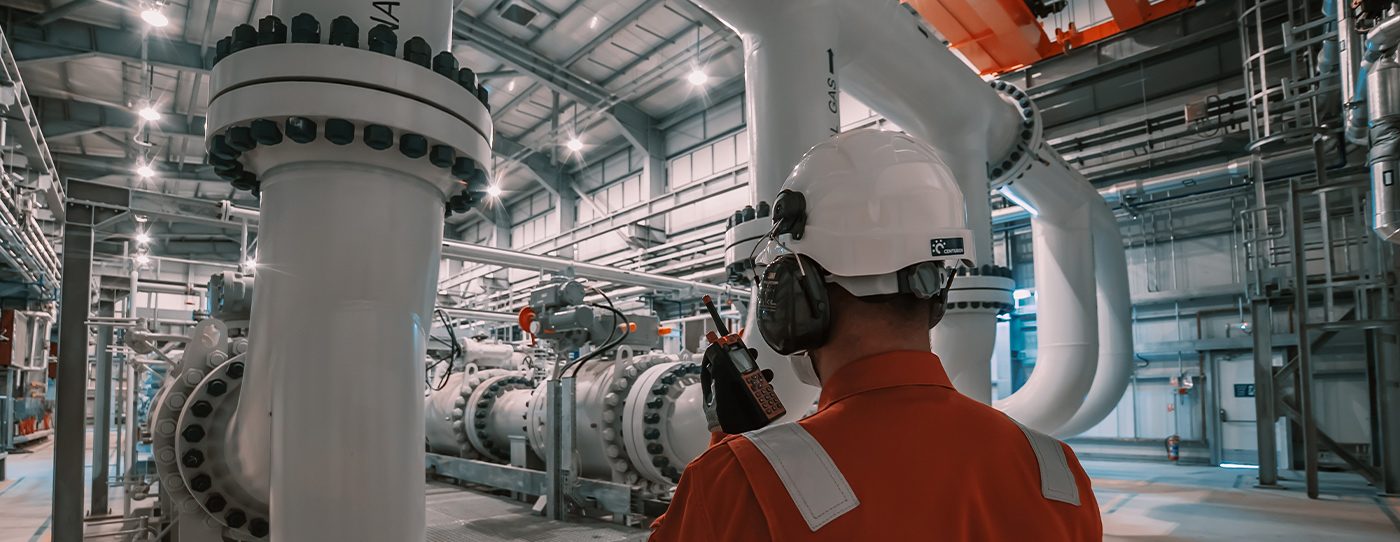
Zero Defect Facilities Guide: What is 5S and How to Implement It?
In the world of business, the quest for high efficiency has persisted from the past to the present. Businesses often seek innovative solutions to boost their productivity. Various methods, including process improvement, a skilled workforce, and digital transformation, are employed for this purpose. Additionally, the workplace environment's impact on productivity is a crucial consideration. A clean and well-organized workspace can yield positive outcomes for both the company and its employees. This systematic approach to creating order is known as the 5S method. In this article, we provide insights into what 5S is and how to implement it. Enjoy your reading!
What is 5S?
The 5S methodology, developed in Japan, is a process management model employed to streamline work structures, boost productivity, and ensure workplace safety in facilities. It derives its name from the five fundamental principles represented by initial letters in Japanese: Seiri (Sort), Seiton (Set in Order), Seiso (Shine), Seiketsu (Standardize), and Shitsuke (Sustain). 5S method involves a meticulous review of items in the workspace, removing unnecessary elements. It also entails the rationalization of work processes, regular cleaning, and the continual repetition of this cycle. Each step contributes to creating a more organized, clean, secure, and efficient work environment for businesses.
“5S method involves a meticulous review of items in the workspace, removing unnecessary elements.”
How to implement 5S?
The 5S method is formed by the sum of the concepts included in its name. Its implementation is quite effortless. Evaluated in a wide range of settings, from small offices to large facilities, 5S can yield successful results when maintained continuously.
Here are the stages of the 5S method:
Seiri (Classification)
The first step, known as Seiri, starts with a thorough review and categorization of workplace needs. Its objective is to declutter the facility and boost efficiency. To begin, it's crucial to identify and categorize the items and materials used in the workspace according to their requirements. This ensures that only the materials needed for the task at hand are readily available, promoting more efficient use of the workspace.
Seiton (Editing)
In the Seiton stage, the items classified in the first step are systematically organized for easy access. This step's primary goal is to optimize workflow and minimize unnecessary time losses. Assigning a specific place for each item in the workplace allows for quick retrieval when needed. This not only accelerates workflow but also minimizes time wastage, leading to increased productivity and reduced errors.
Seiso (Cleaning)
The Seiso step focuses on keeping the workplace clean and organized. A clean workplace not only enhances workplace safety but also helps equipment operate efficiently for longer periods. This stage covers visible dirt as well as hidden contamination and potential hazards. By establishing cleaning routines, the workplace can be maintained in a hygienic and orderly state. Particularly in production lines or laboratories, the importance of regular equipment maintenance and routine cleaning is significant. This is because cleanliness not only provides a pleasant appearance but also significantly affects elements like workplace safety, equipment lifespan, and product quality.
Seiketsu (Standardisation)
Seiketsu aims to establish a lasting culture of the 5S method within the organization. It is concerned with ensuring the continuity of the processes initiated in the first three steps. Additionally, it promotes a realistic perspective where order and cleanliness within the organization are not just routine but also a norm. This enables everyone to adhere to the same rules and procedures, making it easier to anticipate workflow. In addition this step can facilitate the adaptation of new employees to the 5S method.
Shitsuke (Discipline)
The final step, Shitsuke, is crucial for monitoring the other four steps and ensuring their sustainability. The aim of this stage is to maintain order and cleanliness in the workplace because for the 5S method to become a standard in the facility, it must be consistently applied by employees in a disciplined manner. In this method, inspection is not only vertical but also horizontal, where employees check one another and continuously apply these principles, which leads to success.
In summary, the 5S method is a comprehensive approach that helps businesses create a more organised, clean and efficient working environment. Each step contributes to improving safety, reducing errors and optimising workflow. In this way, businesses can use resources more efficiently, improve product quality and employee motivation.
At SOCAR Türkiye, we act with a sustainability approach that aims to create value for our stakeholders in all our processes and considers social development. With our subsidiary Petkim, we became the first company in Türkiye to integrate the 5S method into our sustainability efforts. In 2022, we implemented the "Capacity Increase and Carbon Footprint Reduction Project with the 5S Implementation Project in Product Packaging and Storage Sites". With our project, we were deemed worthy of winning the Silver Award for the Successful Team of the Year in the competition organised by the Turkish Quality Association. We will continue to pioneer innovations in our entire production and economic cycle with our sustainability approach.
We are working today for a better tomorrow, fueled by our energy.