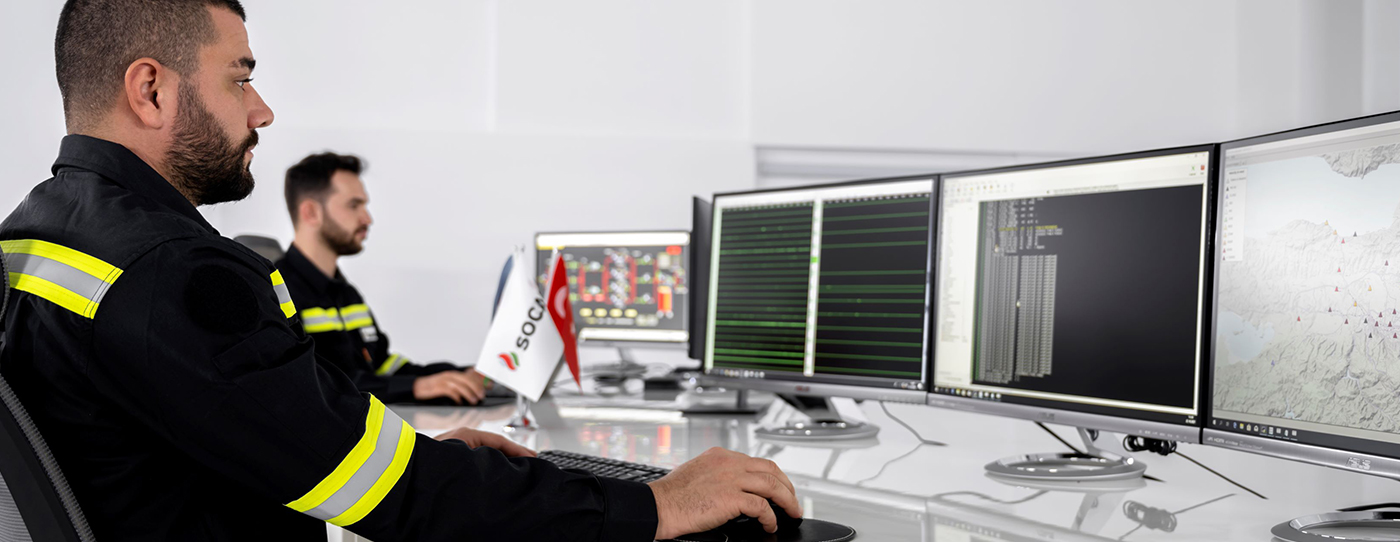
What is Industry 4.0? What are The Benefits for Companies?
As technology advances rapidly, industries are undergoing substantial and transformative shifts. A fresh epoch is unfolding in the domain of industrial manufacturing, labeled as 'Industry 4.0.' However, the precise definition of Industry 4.0, a term intricately linked with the automation and digitalization of factories and production methods, remains to be explored. What advantages does it grant upon businesses? Let's embark on a journey to uncover the responses to these inquiries collectively.
What is Industry 4.0?
Industry 4.0 represents the rise of intelligent manufacturing plants achieved by incorporating digital technologies into production processes. During this period, the merging of tangible and digital systems results in production procedures becoming increasingly adaptable, productive, and automated. Foundational to Industry 4.0 are technologies like the Internet of Things (IoT), artificial intelligence, 5G, extensive data analysis, and cloud computing.
In order to gain a deeper comprehension of the notion of Industry 4.0, let's rewind the narrative. The industrial revolutions stand as pivotal moments in the annals of human history. Commencing with Industry 1.0, the application of steam-powered machinery instigated mechanization. Subsequently, Industry 2.0 witnessed the evolution of mass production methodologies propelled by electricity. With the ascent of computer technology during Industry 3.0, automation and digitalization assumed precedence. Presently, in the era characterized by Industry 4.0, the convergence of digital technologies, artificial intelligence, the Internet of Things, and technologies such as 5G can materialize as intelligent manufacturing plants and streamlined production processes. These revolutions confer upon enterprises production possibilities that are not only more efficient and adaptable but also sustainable. The trajectory of technological advancement assists companies in augmenting their competitive prowess and attaining their sustainability objectives.
The Internet of Things
With the advent of Internet of Things (IoT) technology, machines, devices, and manufacturing elements link up through networks that facilitate communication among themselves and with humans. This connectivity fosters heightened data sharing and collaboration, enhancing the ease of monitoring and controlling processes. For example, within a smart agriculture context, machines can employ sensors to track soil moisture, plant development, and weather conditions. The amassed data can then furnish farmers with real-time suggestions pertaining to plant nourishment, irrigation, and disease management.
Artificial intelligence and automation
Utilizing artificial intelligence algorithms aids in the optimization of production processes, improvement of quality control, and facilitation of automated decision-making. Production efficiency is elevated through the implementation of robots and automation systems, which curtails the need for extensive human involvement. By leveraging AI-driven predictive models, a food manufacturer can achieve heightened precision in forecasting demand. Consequently, this capability fosters refined production planning, equilibrium in stock levels, and enhanced responsiveness to customer needs. Moreover, the deployment of AI-driven physical robots can accelerate material handling tasks along the production line, freeing up workers to concentrate on more strategic duties.
Big data analytics
Extensive amounts of data derived from production processes undergo analysis to convert them into valuable insights utilized within decision-making systems. These insights contribute to process improvement, preemptive identification of potential hardware malfunctions for maintenance planning, and the streamlining of decision-making procedures. Through the application of big data analytics to scrutinize data collected by smart meters, an energy company can detect patterns in energy consumption and uncover potential avenues for energy conservation via these evaluations.
Digital twins
Digital twins, characterized as digital duplicates of tangible objects, find application in simulating and refining production processes. By incorporating real-time data flow, enhancements to processes and early identification of errors become attainable. For example, an energy facility can oversee the condition of turbines and generators in actual time by means of digital twins. This capability allows for the prediction of malfunctions, streamlines the execution of planned maintenance, and mitigates production losses stemming from abrupt interruptions.
What benefits does Industry 4.0 offer to companies?
Industry 4.0, equipped with the mentioned attributes, delivers a plethora of benefits to enterprises, presenting avenues for gaining a competitive edge. The most notable advantages in this regard include:
Efficiency
With the integration of automation and digitalization, production processes accelerate and enhance efficiency. Real-time data is gathered by sensors and smart devices, allowing for the real-time tracking of production line statuses and immediate enhancements in efficiency. Improved resource utilization leads to cost reduction, while simultaneously optimizing production processes.
Flexibility
In the realm of Industry 4.0, companies are presented with the chance to infuse flexibility and tailored approaches into their manufacturing procedures. Intelligent production lines possess the ability to swiftly adjust to alterations in production requirements, thereby streamlining the creation of diverse products on a shared assembly line. This grants businesses the edge of promptly addressing customer needs and delivering bespoke products.
Quality control
Artificial intelligence and big data analytics can be harnessed to elevate the caliber of production procedures. Enterprises have the capacity to oversee machinery conditions and anticipate potential glitches proactively through the utilization of sensors and analytical algorithms. This proactive approach enables preventative maintenance, averting unforeseen machine interruptions caused by unanticipated malfunctions. With errors being swiftly detected and averted, there's a concurrent improvement in product quality.
Sustainability
Industry 4.0 contributes to improved environmental sustainability through the enhancement of energy and resource efficiency. Intelligent production lines and applications based on the Internet of Things (IoT) actively monitor production processes, thereby optimizing the utilization of resources such as energy, water, and raw materials. This capacity facilitates the reduction of environmental effects through the implementation of intelligent energy and waste management techniques.
The technology of Industry 4.0 furnishes businesses with an environment for manufacturing that is not only more efficient, but also offers increased flexibility, customization, and competitiveness. Companies that adopt technologies such as the Internet of Things, artificial intelligence, big data, and digital twins have the potential to elevate their operational performance, decrease expenses, and secure a competitive advantage. For enterprises aspiring to navigate the evolving manufacturing landscape, Industry 4.0 represents a pivotal path of transformation.
Leading the Changing World
At SOCAR Türkiye, we are proud to not just conform to the evolving world, but also to take a proactive role in driving these changes. We incorporate technology, a pivotal element for efficiency and sustainability, across all our operational sectors, with digitalization positioned at the heart of our processes. The awards we've garnered stand as evidence of our accomplishment in harmonizing with the dynamic world around us.
Petkim, serving as Türkiye's inaugural and singular integrated petrochemical company, was singled out as the exclusive Turkish entity to be included in the 'Global Lighthouse Network.' This network, established by the World Economic Forum (WEF), acknowledges establishments that excel in implementing the Industry 4.0 standard, as observed in the year 2020. In the subsequent year, our STAR Refinery unit, demonstrating exceptional prowess in Industry 4.0 technologies, attained the distinction of being the sole Turkish entity selected for the Global Lighthouse Network. Concurrently, it secured the distinction of being the solitary refinery worldwide to achieve such a status. Through perpetuating our pioneering stature within the sector, we seamlessly integrate state-of-the-art technologies into our operational frameworks, culminating in the provision of societal, economic, and environmental advantages that underpin sustainable living. Fueled by the energies of today, we diligently forge the pathways for tomorrow.